GS-ECO 577A™
Is an Undiluted Pure High Solids all Acrylic Latex Polymer manufactured specifically for Gulfstream Mfg. to meet our customers highest standards.
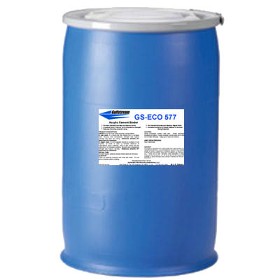
GS-ECO™ Is an All Acrylic Latex additive that has more than one quality!
Manufactured in the USA.
In New Work it can be mixed into cement to:
- Increase Bond Strength
- Flexural Strength
- Increase Compressive Strength
- Reduce Crazing and Cracking
- Allow a 7 Day Dry Cure
- Better Cement Hydration
- Reduce Permeability in Cured Product
In Repair Work it can be used to:
- Increase Adhesion of Cementitious Repair Material
GS-ECO™ 577A works very well with colored concrete products and will not yellow out or discolor your cementious products.
When mixed into GFRC thin section cement batches, it adds to the adhesion properties when being applied to various mold surfaces and creates an extremely homogeneous and highly workable mix.
Until the introduction of the acrylic polymer, GFRC products required a seven day cure in over 95 percent humidity in order to insure full curing of the Portland cement. This usually meant building wet rooms where the product could be stored in the required wet environment.
Where manufacturing was done in an enclosed building, the provision of a curing area resulted in the loss of valuable production space. Where manufacturing was essentially performed outside, the provision of a satisfactory curing area was difficult, if not impossible.
GS-ECO™ polymer eliminates the need for the wet curing period and the associated costs of curing areas and lost production space. These cost savings more than offset the added cost of incorporating GS-ECO™ in the mix.
GS-ECO™ provides added workability to the GFRC mix, particularly better adherence to vertical mold surfaces, so reducing the tendency of the wet mix to slide. It's suitable for use with both white and gray Portland cements.
GS-ECO™ does not yellow when weathered, and is it will not discolor panel finishes, as some acrylic polymers can do.
Because GFRC is mucher thinner in cross section as compared to conventional concrete. GFRC without polymer can lose water by evaporation too quickly. GFRC composites use to have to be stored in a wet environment to maintain sufficient water in the composite and ensure complete hydration of the cement.
GS-ECO™ when added to GFRC mixes at the recommended level, does not change the hydration process of Portland cement. It’s function is to reduce permeability during the first few hours of cure, first on the surface by forming a sealing film and then within the composite. This reduced permeability in the composite significantly lessens the loss of water by evaporation, facilitating the full hydration and cure of the Portland cement.
Excessive loss of water during curing, to such an extent that there’s not sufficient water remaining to fully hydrate the Portland cement, will result in low cement and composite strengths. Further, there are no remedial procedures that will retrieve the composite strengths if the initial cure is not done correctly.